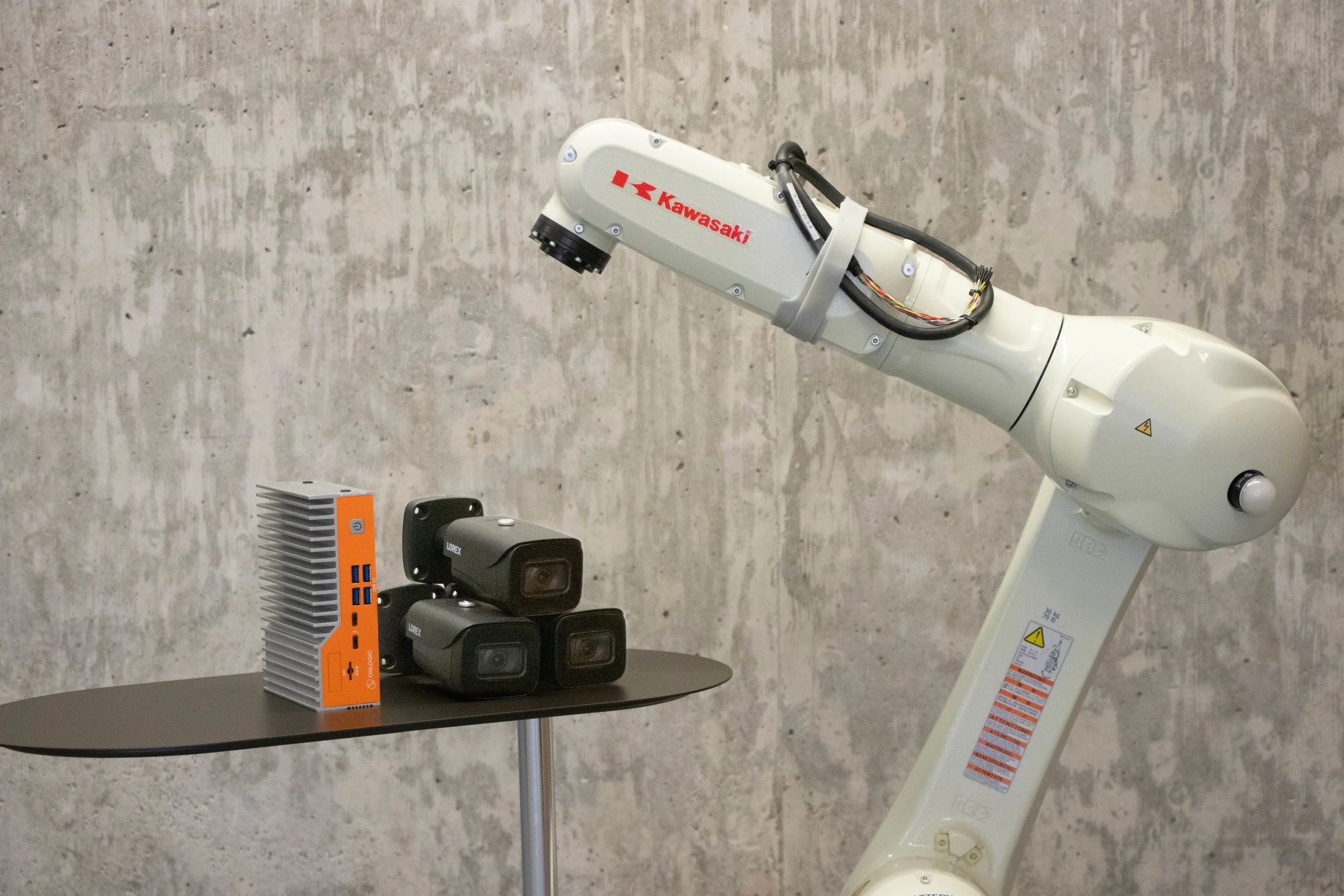
Video-based diagnostics for Kawasaki Robots
Errors happen in manufacturing facilities.
Common errors such as a part improperly oriented in the machine or a slight deflection in a robot’s path can bring production to a grinding halt, costing you time and money. But in an unattended production environment, quickly fixing the issue and restarting production is a challenge because there is no one on the shop floor to address the problem and get things moving again.
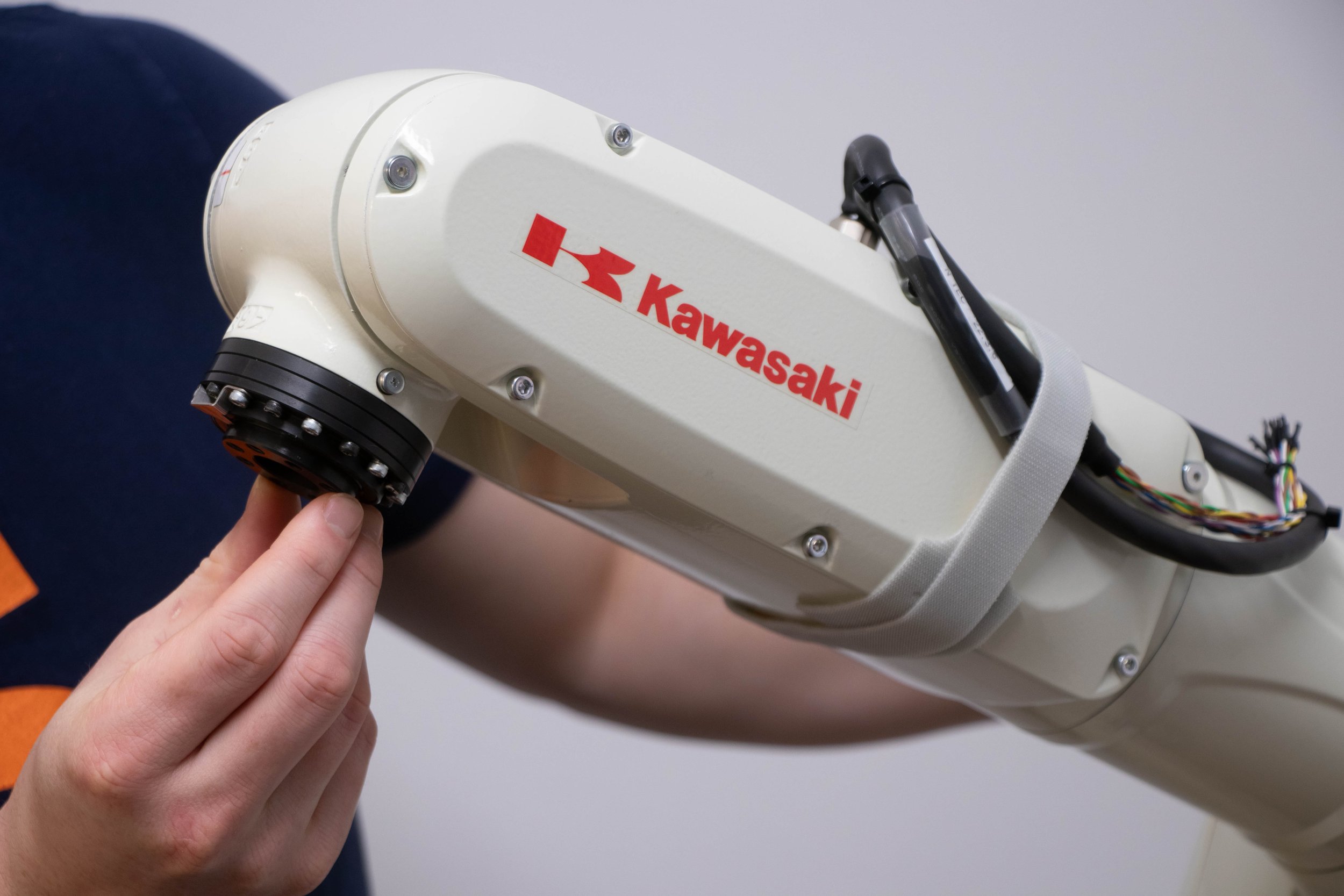
Diagnostics for any application
Machine tending
Assembly
Palletizing
Finishing
Quality inspection
Material removal
Video-based diagnostics for Kawasaki Robots
MONITOR
Records all telemetry and streams up to 8 Power-over-Ethernet (PoE) live feeds from your cell
DIAGNOSE
Collects video and log snapshots whenever a downtime event occurs, providing automation experts with the information they need
RESOLVE
Lets you tackle the root-cause of the problem and add event triggers to ensure the issue remains fixed
Reduce the Impact of the Labor Shortage
Without remote monitoring and control, your robot applications would require onsite personnel to address production issues. That means finding more skilled labor in an already depleted labor market or placing additional burdens on your current workforce, neither of which are conducive to efficient, productive and cost-effective manufacturing.
Using Olis remote monitoring and control not only relieves this burden on workers but frees your workers to complete higher-value tasks that further boost productivity and efficiency while reducing waste while one worker monitors the progress of the robots. This doesn’t just improve your bottom line, but increases worker morale.
